
.jpg)
The planar dynamic stiffness matrices of the piezo-plate, the piezo-stack, and the piezoelectric actuator with insulating plates are deduced by considering PEA as several beam components with external forces equivalent to piezo-actuated forces. Based on piezoelectric vibration theory and dynamic stiffness method, a new modeling method for compliant mechanisms actuated by piezo-stack has been proposed in this work. To design and optimize a stage with high bandwidth and proper motion range, it is necessary to establish a kinetostatic and dynamic model for the piezo-stack widely used in nano-positioning stage. However, this causes large overshoot, which must be compensated for by the controller.įeature image credit: Stack Exchange Inc.Piezoelectric actuator is a critical component of piezo-actuated compliant mechanisms, especially for the precision positioning stage. With a rapid increase in control voltage, a piezo system can typically reach its nominal displacement in 1/3 the period of its resonant frequency. When operated below their resonant frequencies, piezo actuators act like capacitors, with displacement being proportional to the stored charge. However, piezo systems (especially actuators used for positioning) are often operated below their resonant frequencies in order to minimize the phase shift between the driving signal and the actuator. Theoretically, the resonant frequency is the operating frequency at which the piezo material vibrates most readily and converts electrical energy into mechanical energy most efficiently. Minimum impedance (f m) occurs at the resonant frequency and maximum impedance (f n) occurs at the anti-resonant frequency. Maximum response of a piezo system occurs between f m and f n. Piezo systems with a higher resonant frequency will have a better phase and amplitude response, which means that the operating frequency can be higher.
DYNAMIC RESPONSE OF STACK PIEZO ACTUATORS SERIES
The series and parallel frequencies are suitable approximations of the minimum and maximum impedance frequencies – f m and f n, respectively – and therefore are used to determine the parameters of the piezoelectric motor or system. This is also known as the anti-resonant frequency, f a. Conversely, the parallel resonant frequency, f p, in the equivalent circuit occurs when impedance in the circuit is theoretically infinite (assuming mechanical losses are ignored). In an electrical circuit representing the piezo element, the frequency at which the impedance of the circuit is at a minimum is the series resonant frequency, f s. In manufacturer specifications, the resonant frequency given for a piezo actuator assumes that it is unloaded and one end is fixed or attached to a mass that is significantly larger than the actuator.į 0‘ = resonant frequency with added mass (Hz) In addition, attaching a load to a piezo motor or actuator reduces its resonant frequency – the higher the load, the more the resonant frequency is reduced. For example, a thicker piezo element will have a lower resonant frequency than a thinner element of the same shape. The resonant frequency of a piezo motor or actuator depends on its material composition, shape, and volume.
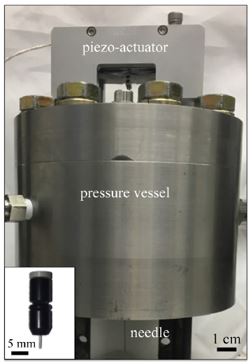
When damping effects are small, the resonant frequency of the system is approximately equal to its natural frequency.į 0 = resonant frequency (without load) (Hz) When one oscillating object or system (a piezo drive or controller) drives another system (a piezo motor or actuator) at or near the natural frequency of the second system, the second system will oscillate at a high amplitude at a specific frequency. This causes the object or system to vibrate strongly and can result in unexpected – and sometimes catastrophic – behavior. Resonance occurs when the resonant frequency (also referred to as the natural frequency) of an object or system is equal or very close to the frequency at which it is being excited.
